Enamel Pin Guide
Not sure how to design an enamel pin? This comprehensive guide will tell you everything you need to know about turning your artwork into a custom enamel lapel pin!
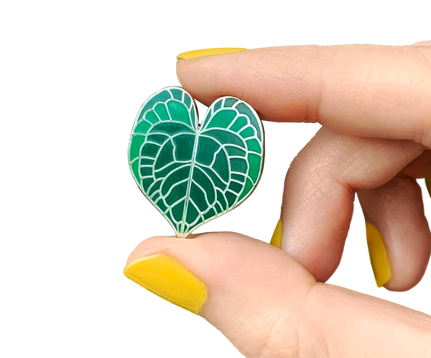
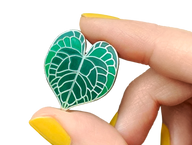
Designing Custom Enamel Pins
Step 1
We receive your pin request
While vector art is preferred, if you take away anything from this guide it's that WE ACCEPT ANY FILE TYPE. Most customers need to modify their art so the easiest way to kick things off is to just submit your file in whatever format you have available. Even a concise description of your design (i.e. "I want a blue heart with the text 2021 in silver metal") is a great starting point!
Placing an order through the website and attaching the artwork as a file upload is the best way to send it. Alternatively, you can email sales@wizardpins.com with artwork.
We typically can respond within the same business day but outside of a few rare cases, it won't be more than 24 hours
Yes! That actually can sometimes be super helpful in sketching out the placement of different elements.
Yes, of course! Sometimes, our art upload tool has trouble with multiple files so it's best to upload what you can and then respond via email with additional assets.
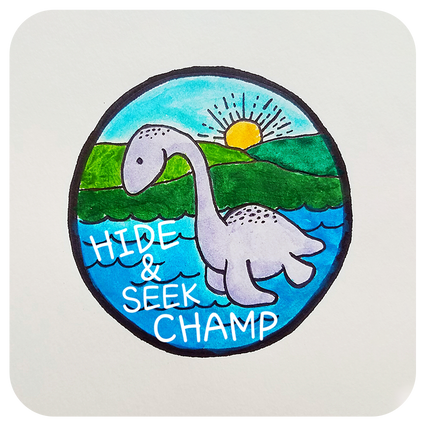
Step 2
Our team creates line art
Our talented team of artists will recreate your design as a line drawing to work with the enamel process. The white areas represent cavities that can be filled with enamel and the black lines represent the metal portions of the pin. Some designs require a lot of simplification (ex. photographs) whereas others that are set up by graphic artists can be reproduced exactly as shown. Every design is a bit different!
Raster images are comprised of tiny pixels that when grouped together, form a larger image. When zooming in on a raster image, you'll notice they become more blurry. On the other hand, vector art, typically built in Adobe Illustrator, scales infinitely and looks smooth and sharp even when you enlarge the image. Most customers submit raster images which need to be converted (by our team) to vector.
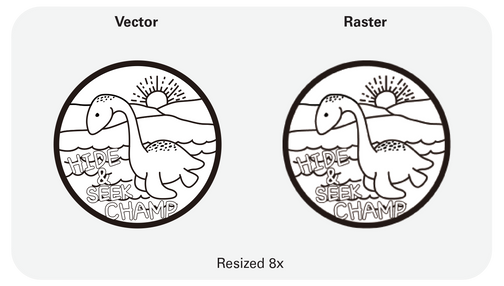
There's a limit on what can be included in the mold use to strike the pins out of metal. In these instances, the details typically are omitted because they wouldn't register on the final product.
-No gradients or shading -Each color is outlined by metal -Minimum metal line thickness is 0.2mm and the minimum color area is 0.3mm -Text has to be at least 5pt. -Simple designs are best
Each pin is created custom to your order so there's no standard template. Looking to make a 1" pin? A good rule of thumb is to draw something or prepare a file that looks legible when scaled down to 1".
We don't reproduce artwork if you don't have the IP rights or proper licensing. We also won't make designs that advocate hate speech.
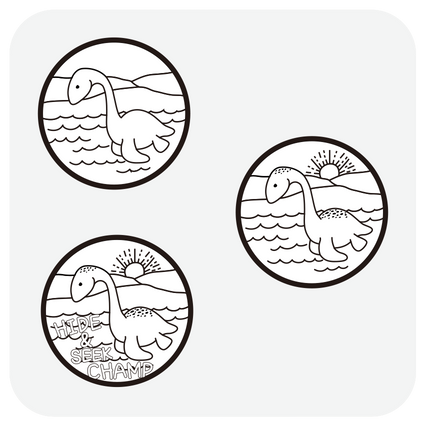
Step 3
We select Pantone colors and a metal tone
The Pantone color system provides a wide range of premixed and numbered colors, allowing for us to choose enamel colors that match your designs. Additionally, this is the stage where we choose a plating option that will serve as the base metal for your pin.
To best understand how the colors will look in person, we recommend getting a physical swatch book for uncoated Pantone colors. Soft enamel tends to work better for color matching whereas some colors on hard enamel pins look somewhat muted (ex. yellows, oranges) due to the polishing process. If matching your brand colors is challenging for other promo products, we'd recommend doing a sample for approval.
Yes, if you submit a raster file or don't have official brand colors, our team will automatically choose colors that best match your design. If you have specific colors that you'd like to use, please let us know.
We don't suggest using more than 8 colors. We've found that designs with more colors typically are too complex to be enameled and are better suited for a printed process. If you really need more than 8, please bring this up in the proofing process and we can confirm how much more expensive it'd be to accommodate.
No, we can't use CMYK/Hex for enamel but our team can match the closest equivalent in the Pantone library.
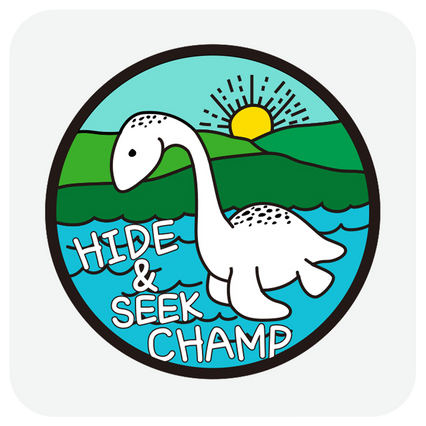
Step 4
We share a digital mock-up
Your design is finally coming to life and we put together a production sheet to show how we could make your design. This is meant to be a starting point and at this stage you'll see the size, front/back, plating options, PMS colors and attachment we would use for your project.
We have a legend for both the PMS colors and plating used for your design. Looking at the reverse side of the pin will show you the metal plating we'll use for the pin.
For pins, the most default option is our black rubber PVC clutch. We've found that is the most consistent backer but if you prefer a butterfly clutch (silver or gold) we can do those for no extra charge. If you want a magnetic backing, that can be added on the cart page at checkout.
Custom backstamps are a flat fee of $49.99 and can be used on future designs as long as they fit. By default, we put on our WizardPins logo on the pin but can remove it if you ask.
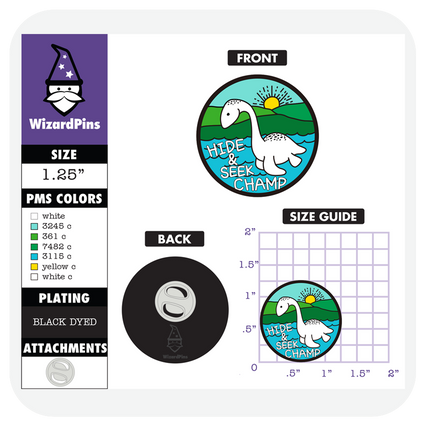
Step 5
You provide feedback until you approve the design
Most customers require a few rounds of feedback before approving the artwork. It's not uncommon to go through several rounds of revisions, but things typically can go faster if you concisely list the changes you need. The most common changes are to the size, metal plating and colors.
After producing several thousand custom orders for customers, we've found the key to a quick proofing process is clear communication. Listing your feedback in bullets and clearly defining requests (ex. Change PMS 185 to PMS 135) will go a long way to expediting the process. Marking up a file in an editing program can also help remove ambiguity.
Nine out of ten times, the change isn't possible. Sometimes customers want additions or updates to designs that don't work with the production process.
Small text + details in color sometimes need to be converted into metal lines (or removed completely) to work with this process. If preserving all colors is absolutely required by your branding team, we have other printed styles that can work with any file.
In order to accommodate more detailed designs, the easiest way to set up the art and maintain most of the detail is to use a larger pin size. A lot of customers will select the smallest size and ask for an extremely complex design. If increasing the size isn't an option, some of the detail needs to be removed to make a smaller pin.
We include a size grid showing exactly how large the pin will be. When we list a size, we're using the longest dimension between the height and width. Our most popular size is 1".
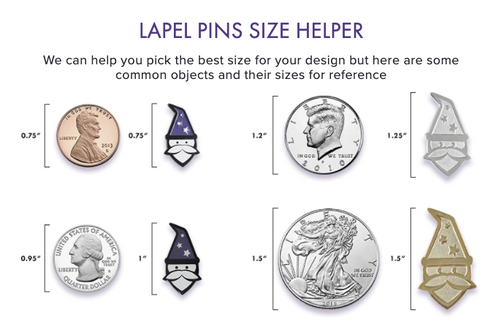
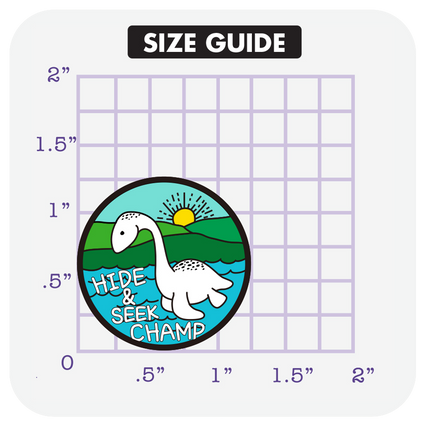
Final Step
We make the pins and ship them to you!
Once you give us the green light, we'll start producing the pins per the approved proof. Give us a few weeks to make them and then we'll share a tracking number to the email used to place the order.
Our average production time is approximately 2 weeks. Since most of our enamel pins are shipped from China, transit can be anywhere from 1-2 business days to more than a week. If you have a rush deadline, please alert our team at the start of the project.
Given the custom nature of our production process, once you approve a design, we start manufacturing immediately and don't have the option to modify a design.
The majority of our orders ship via FedEx in secure cartons. Unless instructed otherwise, we individually polybag each pin and master bag in 50s or 100s for most orders.
Email the order thread we've been using to communicate about your proof and we'll work with you towards a solution! To proactively avoid any issues, we strongly recommend samples for approval if time permits.
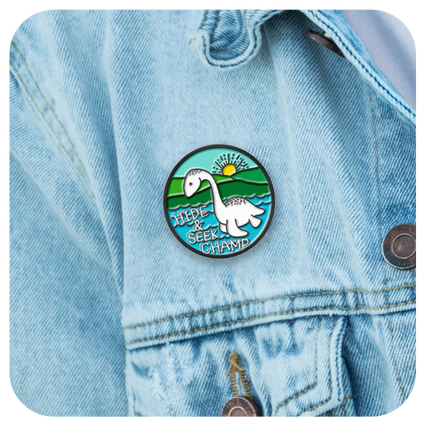